Table Of Contents:
- Introduction to the Role of Welding in Auto Body Repair
- Traditional Welding Techniques Used in Auto Body Work
- Factors Driving the Evolution of Welding Techniques
- Modern Welding Techniques Revolutionizing Auto Repair
- The Integration of Technology in Welding Equipment
- Training and Skill Development for Modern Welders
In the world of auto body repair, welding techniques have undergone a significant transformation. From traditional methods to cutting-edge technologies, the evolution of welding has revolutionized how vehicles are repaired. This article explores the journey from gas tungsten arc welding to laser beam welding, examining how factors like voltage, paint considerations, and advanced tools have shaped modern auto body repair practices. Readers will gain insights into the latest welding techniques, understanding how these advancements improve repair quality and efficiency.
Introduction to the Role of Welding in Auto Body Repair
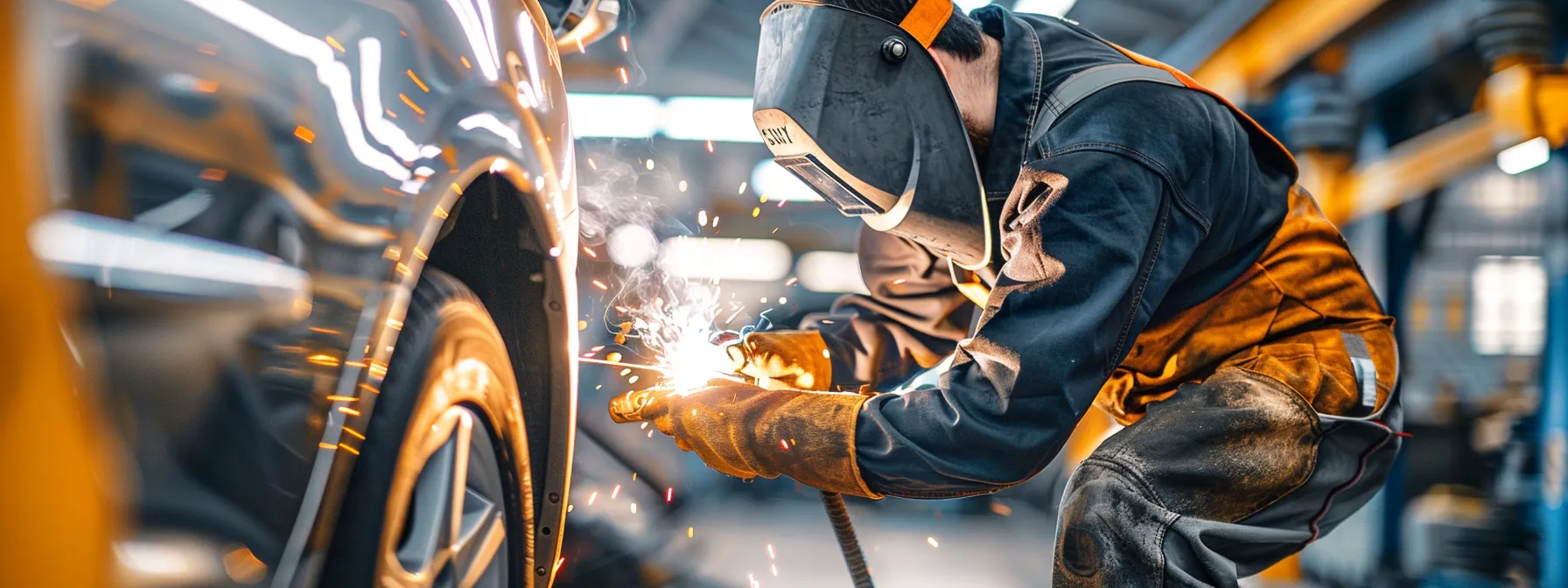
Welding plays a crucial role in modern auto body repair, ensuring vehicle structural integrity and safety. This section explores the evolution of welding techniques, from early practices to contemporary methods. It examines how welding affects the base metal, the impact of heat on vehicle components, and the integration of advanced technologies like laser welding and adhesive bonding in wheel and body repairs.
How Welding Ensures Vehicle Structural Integrity
Welding plays a critical role in ensuring vehicle structural integrity during auto body repair. By fusing sheet metal components, welding creates strong, durable joints that maintain the vehicle's original strength and safety specifications. This process is particularly crucial when repairing or replacing damaged sections of the vehicle's frame or body panels.
In the automotive industry, welding techniques have evolved to address the specific needs of modern vehicles. Advanced steel alloys and specialized welding methods allow technicians to repair or replace structural components without compromising the vehicle's overall integrity. This is especially important for critical safety areas such as the bumper and passenger compartment.
The use of welding in auto body repair extends beyond simple metal fusion. It also involves the careful application of heat shielding techniques to protect surrounding components from thermal damage. By precisely controlling the welding process, skilled technicians can restore a vehicle's structural integrity while preserving its original design and safety features.
Early Welding Practices in Automotive Repair
Early welding practices in automotive repair primarily relied on oxy-acetylene welding techniques. This method involved using a mixture of oxygen and acetylene gases to create a flame hot enough to melt and fuse metal components. While effective for joining steel parts, it posed challenges when working with thinner, more corrosion-prone materials used in vehicle bodies.
As vehicles evolved, incorporating more stainless steel and plastic components, welding techniques had to adapt. The introduction of arc welding, particularly MIG (Metal Inert Gas) welding, marked a significant advancement in auto body repair. This process utilized a wire electrode and shielding gas to create stronger, more precise welds, especially useful for repairing thinner gauge metals.
The transition from traditional welding methods to more specialized techniques became necessary as vehicle designs grew more complex. Early practices often resulted in excessive heat application, potentially compromising the integrity of surrounding materials. This led to the development of spot welding and other localized heating methods, which minimized heat-affected zones and improved overall repair quality.
- Oxy-acetylene welding: Early standard technique
- Introduction of arc welding: Improved precision and strength
- Adaptation to new materials: Stainless steel and plastic components
- Development of spot welding: Reduced heat-affected zones
- Transition to specialized techniques: Enhanced repair quality
The welder's torch flared to life, its blue flame dancing across the damaged metal. With steady hands and practiced precision, the technician began the delicate process of fusing the broken pieces back together.
Traditional Welding Techniques Used in Auto Body Work
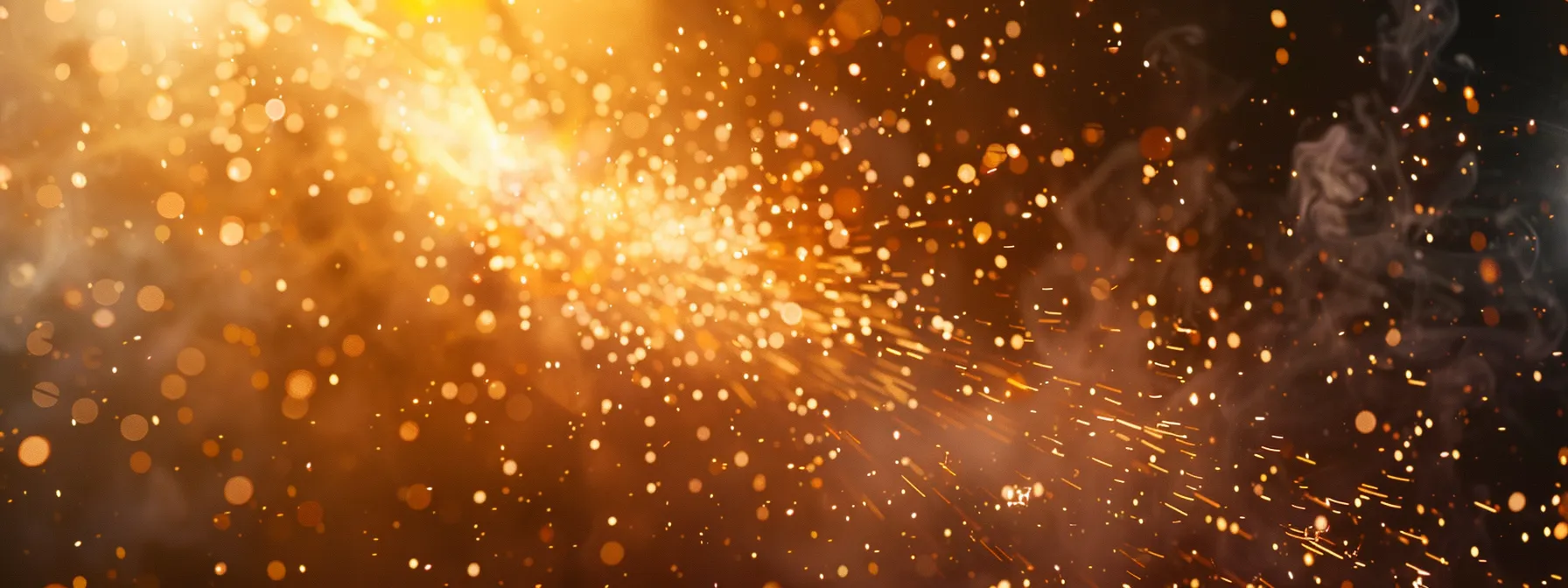
Traditional welding techniques in auto body work encompass various methods, each with specific applications and limitations. This section explores oxy-acetylene welding, resistance spot welding, and conventional welding methods. It also touches on related processes like brazing, arc welding, and plasma cutting, as well as the use of fasteners and adhesives in modern auto body repair.
Oxy-Acetylene Welding and Its Applications
Oxy-acetylene welding remains a valuable technique in auto body repair, particularly for its versatility in handling various metals and thicknesses. This method utilizes a mixture of oxygen and acetylene gases to generate intense heat, allowing technicians to join metal components effectively. In modern auto body shops, oxy-acetylene welding complements advanced technologies, proving especially useful for repairing older vehicles or custom fabrication work.
While newer welding methods have emerged, oxy-acetylene welding continues to play a role in specific auto body applications. For instance, it excels in repairing gear mechanisms in classic cars or riveting components in vintage vehicle restorations. The precision and control offered by this technique make it suitable for delicate work on thin metal sheets, which is crucial in maintaining the structural integrity of the vehicle.
As the automotive industry evolves, including the rise of electric vehicles, oxy-acetylene welding adapts to new challenges. In manufacturing and repair processes for electric vehicles, this welding method finds applications in areas where high-tech welding machines may not be suitable. Its flexibility allows technicians to perform repairs on various components, from body panels to intricate parts of the electric powertrain, ensuring the longevity and safety of modern vehicles.
Resistance Spot Welding Fundamentals
Resistance spot welding is a fundamental technique in modern auto body repair, utilizing electrical resistance to generate heat and fuse metal surfaces. This method proves particularly effective for joining thin metal sheets, making it ideal for repairing vehicle body panels and structural components. Unlike gas metal arc welding, which requires shielding gases like argon or carbon dioxide, resistance spot welding operates without the need for additional gases or filler metals.
The process involves pressing two metal pieces together between copper electrodes and passing a high-amplitude electric current through them. The resistance at the contact point generates intense heat, creating a molten nugget that solidifies to form a strong weld. This technique is widely used in automotive manufacturing and repair due to its speed, efficiency, and ability to produce consistent results across multiple welds.
While resistance spot welding excels in joining sheet metal, it has limitations when working with thicker materials or tanks. In such cases, other welding methods like gas metal arc welding might be more suitable. However, for standard auto body repair tasks, resistance spot welding remains a cornerstone technique, offering a balance of strength, speed, and precision that is essential in maintaining vehicle structural integrity.
Limitations of Conventional Welding Methods
Conventional welding methods, while effective for many auto body repair tasks, face limitations when working with modern vehicle materials. The electric arc used in traditional welding can generate excessive heat, potentially warping thin metal panels or damaging sensitive electronic components in newer cars. This heat-related issue becomes particularly problematic when repairing vehicles with advanced high-strength steel or aluminum bodies.
Another limitation arises from the difficulty in welding dissimilar metals, a common requirement in modern vehicle construction. Conventional techniques may struggle to create strong, durable bonds between different metal types, such as steel and aluminum. This challenge often necessitates the use of specialized equipment or alternative joining methods, impacting repair costs and time.
The increasing complexity of vehicle designs also poses challenges for conventional welding. Tight spaces and intricate assemblies can make it difficult for technicians to access weld points with traditional equipment. Additionally, the presence of sensitive electronic systems in modern vehicles requires extra precautions to prevent damage from welding-induced electromagnetic interference. These limitations have driven the development of alternative joining techniques and the adoption of more advanced welding technologies in auto body repair shops:
- Heat-related damage to thin panels and electronics
- Challenges in welding dissimilar metals
- Limited access to weld points in complex designs
- Risk of electromagnetic interference with vehicle systems
- Need for specialized equipment and techniques
The world of auto body repair never stands still. As technology advances, so too do the techniques used to mend and restore vehicles.
Factors Driving the Evolution of Welding Techniques
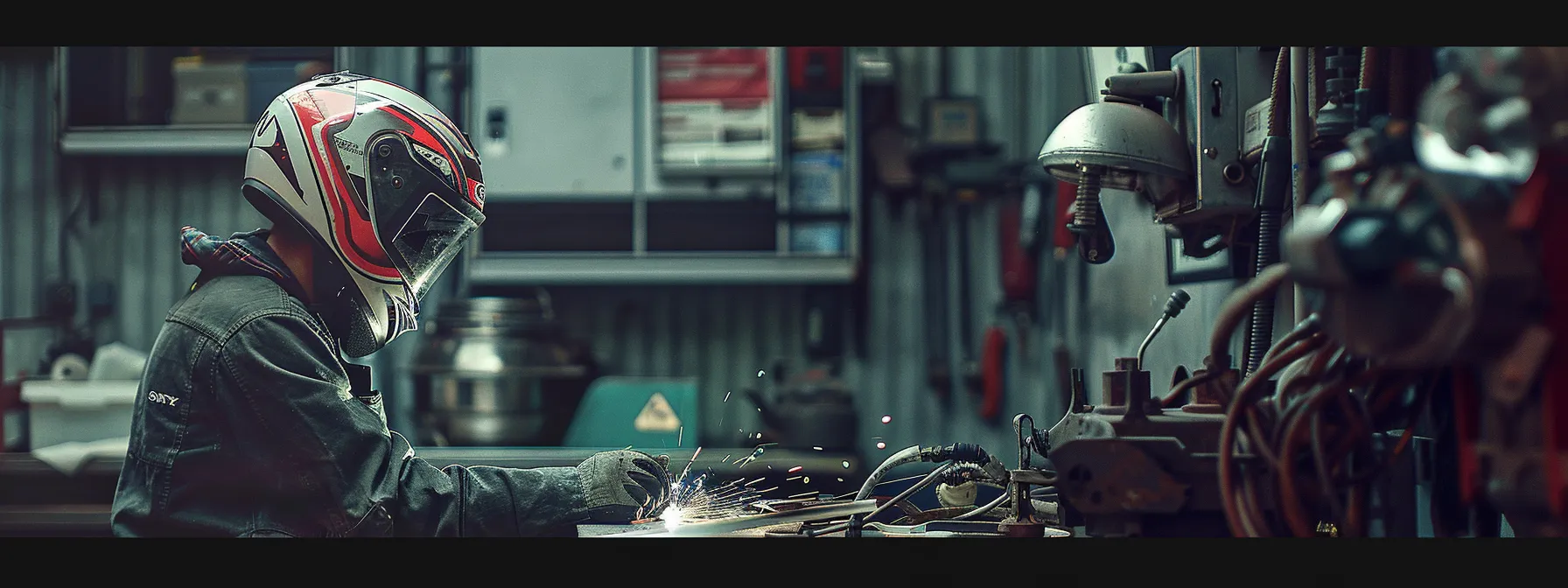
The evolution of welding techniques in modern auto body repair is driven by advancements in automotive materials, demand for stronger and lighter structures, and environmental and safety regulations. These factors have led to innovations in collision repair methods, including spot welding for carbon steel components. Auto mechanics now use specialized helmets and equipment to adapt to these changes, ensuring safer and more efficient repair processes.
Advancements in Automotive Materials and Design
Advancements in automotive materials have significantly impacted welding techniques in modern auto body repair. The introduction of high-strength steels and aluminum alloys in vehicle frames has necessitated the development of new welding methods. Auto body technicians now require specialized training to work with these materials, as traditional welding techniques may compromise the structural integrity of these advanced components.
The use of composite materials in vehicle design has further challenged conventional welding practices. These materials often require alternative joining methods, such as adhesive bonding or mechanical fasteners. As a result, auto body shops have had to invest in new equipment and adapt their repair processes to accommodate these changes, particularly when working on critical components like radiators and vehicle frames.
Modern vehicle designs incorporating multiple materials within a single structure have led to the development of hybrid welding techniques. These methods often combine traditional welding with advanced technologies, such as laser welding or friction stir welding. Auto body technicians must now consider factors like heat input, filler material selection, and shielding gas composition to ensure proper fusion of dissimilar materials while maintaining the vehicle's original structural properties.
Demand for Stronger and Lighter Vehicle Structures
The automotive industry's push for stronger and lighter vehicle structures has significantly influenced welding techniques in auto body repair. Modern vehicles increasingly incorporate high-strength alloys, including magnesium and advanced aluminum compositions, to reduce weight while maintaining structural integrity. This shift has necessitated the development of specialized welding methods that can effectively join these materials without compromising their properties.
Traditional welding techniques, such as shielded metal arc welding, have evolved to accommodate these new materials. Welders now use specialized filler metals and precise heat control to ensure proper fusion and prevent distortion or weakening of the base metal. The introduction of tungsten inert gas (TIG) welding has proven particularly effective for working with lightweight alloys, offering superior control and cleaner welds.
Auto body repair shops have adapted to these changes by investing in advanced welding equipment and training technicians in new techniques. The ability to effectively repair and restore lightweight, high-strength structures has become crucial in maintaining vehicle safety and performance. As manufacturers continue to push the boundaries of material science, welding techniques in auto body repair will likely continue to evolve to meet the demands of stronger and lighter vehicle structures.
Environmental and Safety Regulations Impacting Welding
Environmental regulations have significantly influenced welding techniques in auto body repair. The use of inert gas in processes like plasma arc welding has become more prevalent, as it reduces harmful emissions compared to traditional methods. Auto body shops now prioritize eco-friendly practices, including proper ventilation systems and waste management procedures, to comply with stringent environmental standards.
Safety regulations have led to improvements in welding equipment and personal protective gear. Original equipment manufacturers have developed advanced welding helmets with auto-darkening features and improved respiratory protection. These innovations allow technicians to work more safely when repairing components such as fenders, reducing the risk of eye injuries and exposure to harmful fumes.
The push for safer work environments has also impacted the composition of welding materials. Manufacturers have developed low-fume flux formulations that reduce toxic emissions during the welding process. This advancement not only protects workers but also aligns with environmental regulations, demonstrating how safety and environmental concerns often intersect in modern auto body repair practices.
Welding techniques evolved rapidly, driven by industry demands. Now, modern methods revolutionize auto repair, transforming how vehicles are fixed.
Modern Welding Techniques Revolutionizing Auto Repair

Modern welding techniques have revolutionized auto body repair, enhancing efficiency and precision. MIG welding offers improved speed and versatility, while TIG welding achieves high-quality results. Laser welding brings innovation to automotive manufacturing, and friction stir welding excels in joining dissimilar metals. These advancements require skilled technicians to prevent contamination and ensure proper electrode use, particularly when working on critical components like exhaust systems.
MIG Welding: Enhancing Efficiency and Precision
MIG welding has revolutionized auto body repair by enhancing efficiency and precision. This technique allows technicians to work faster and more accurately, particularly when repairing complex engine components. The use of a continuous wire electrode and shielding gas, often a mixture of argon and carbon dioxide, protects the weld from atmospheric contamination, resulting in cleaner, stronger welds.
One of the key advantages of MIG welding in auto body repair is its versatility. Technicians can easily adjust the welding parameters to suit different metal thicknesses and types, from thin body panels to thicker structural components. This flexibility extends to repairing pipes and exhaust systems, where precise control over heat input is crucial to prevent warping or damage to surrounding parts.
MIG welding also offers improved control over oxide formation during the welding process. By carefully selecting the appropriate wire and gas combination, technicians can minimize the formation of harmful oxides that could compromise the integrity of the weld. This level of control is particularly important when working on critical safety components, ensuring that repaired vehicles meet stringent safety standards.
TIG Welding: Achieving High-Quality Welds
TIG welding has revolutionized auto body repair by achieving high-quality welds on various metal parts. This precision technique uses an electric current to create an arc between a non-consumable tungsten electrode and the workpiece, allowing for exceptional control and clean, strong welds. Auto body mechanics rely on TIG welding for its ability to join thin materials and create aesthetically pleasing results, particularly in visible areas of the vehicle.
The process requires significant skill and attention to detail, with technicians carefully manipulating the torch and filler rod while maintaining a steady hand. A specialized welding helmet with auto-darkening features protects the mechanic's eyes from the intense light produced during the welding process. This level of precision makes TIG welding ideal for repairing delicate components and working with materials that are sensitive to heat distortion.
TIG welding excels in joining dissimilar metals and materials with low carbon content, offering versatility in modern auto body repair. The technique produces minimal spatter and slag, resulting in cleaner welds that require less post-weld cleanup. This efficiency, combined with the high-quality results, has made TIG welding an essential tool for auto body shops working on high-end vehicles or custom restorations where weld appearance is crucial.
Laser Welding: Innovation in Automotive Manufacturing
Laser welding has revolutionized automotive manufacturing, offering unparalleled precision and speed in joining components. This technique proves particularly effective for welding aluminium, a material increasingly used in modern vehicles to reduce weight and improve fuel efficiency. Auto collision repair shops now utilize laser welding to restore damaged vehicles to their original specifications, ensuring structural integrity after a traffic collision.
Unlike traditional welding methods that use a torch, laser welding minimizes heat-affected zones, reducing the risk of warping or weakening surrounding materials. This precision is crucial when repairing vehicles involved in collisions, as it allows technicians to maintain the vehicle's original strength and safety features. The focused heat of laser welding also helps prevent rust formation at weld points, a common issue in areas prone to moisture accumulation.
The adoption of laser welding in auto body repair has significantly improved the quality and efficiency of repairs following traffic collisions. Auto collision repair shops equipped with laser welding technology can achieve factory-quality welds, ensuring that repaired vehicles meet or exceed original safety standards. This innovation has particularly benefited the repair of modern vehicles with complex structures and materials, allowing technicians to perform precise, localized repairs without compromising the vehicle's overall integrity.
Friction Stir Welding: Joining Dissimilar Metals
Friction stir welding has emerged as a revolutionary technique in auto body repair, particularly for joining dissimilar metals. This solid-state welding process uses a rotating tool to generate heat through friction, softening the metals without melting them. Auto body technicians now employ this method to create strong, defect-free welds between materials that are traditionally difficult to join, such as aluminum and steel.
The process offers several advantages in auto collision repair. It produces minimal heat-affected zones, reducing distortion and maintaining the material's original properties. This is crucial when repairing modern vehicles with complex multi-material structures. Friction stir welding also eliminates the need for filler materials, resulting in cleaner, more precise joints that closely match the vehicle's original specifications.
Auto body shops have adapted to incorporate friction stir welding into their repair processes, particularly for addressing damage from traffic collisions. This technique allows for more effective repairs of lightweight vehicle components, contributing to improved fuel efficiency and safety standards. The adoption of friction stir welding represents a significant advancement in auto body repair technology, enabling technicians to meet the challenges posed by evolving vehicle designs and materials:
- Solid-state welding process for joining dissimilar metals
- Minimal heat-affected zones for reduced distortion
- No filler materials required for cleaner joints
- Effective for repairing lightweight vehicle components
- Contributes to improved fuel efficiency and safety standards
The welding shop hummed with modern machinery. New technology transformed old tools, promising better repairs.
The Integration of Technology in Welding Equipment
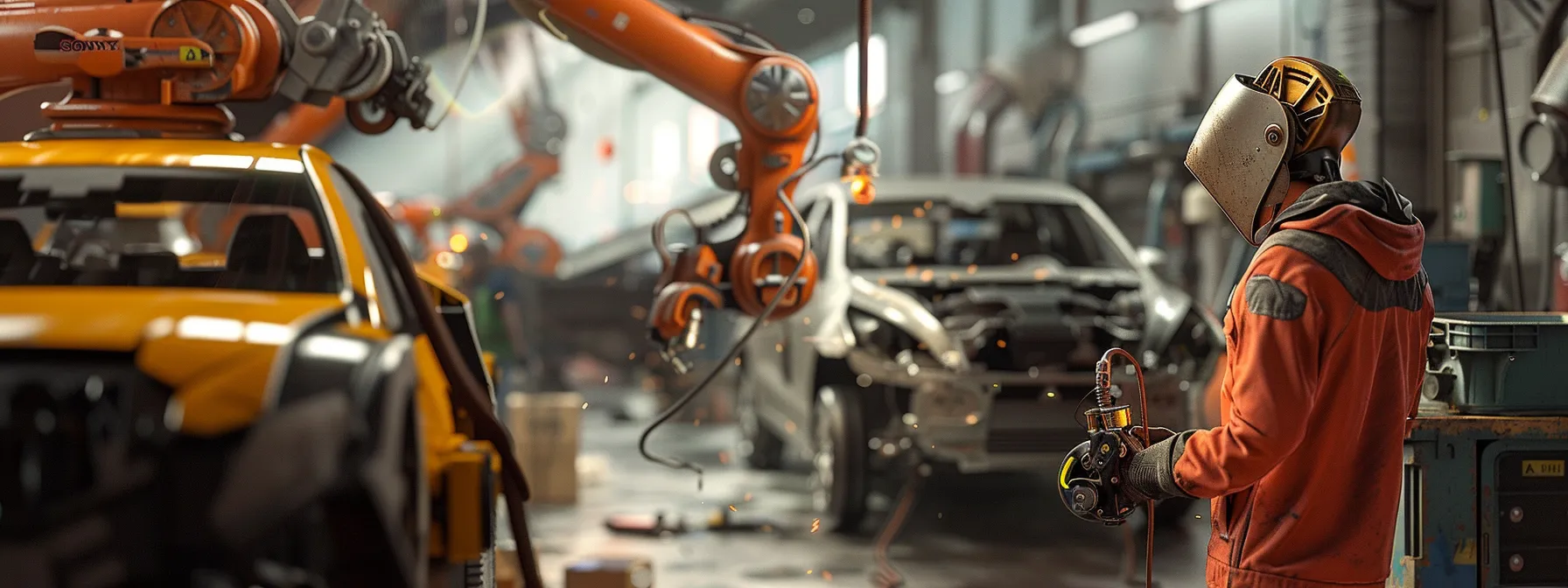
The integration of technology in welding equipment has transformed modern auto body repair. Automation and robotics have streamlined welding processes, while computer-aided systems enhance accuracy. Advancements in protective gear ensure technician safety. These innovations have improved efficiency and precision in auto body shops, meeting the demands of today's complex vehicle repairs.
Automation and Robotics in Welding Processes
Automation and robotics have revolutionized welding processes in modern auto body repair shops. These advanced systems utilize precise sensors and computer-controlled movements to perform consistent, high-quality welds on various vehicle components. By automating repetitive tasks, auto body technicians can focus on more complex repairs, improving overall efficiency and productivity.
Robotic welding systems excel in handling intricate joining processes, particularly in areas difficult for human welders to access. These machines can work tirelessly, maintaining consistent weld quality even during long production runs. This level of precision is crucial when repairing modern vehicles with complex structures and materials, ensuring that repaired components meet original equipment manufacturer (OEM) specifications.
The integration of artificial intelligence and machine learning in robotic welding systems has further enhanced their capabilities. These smart systems can adapt to variations in material thickness, adjust welding parameters in real-time, and even predict potential issues before they occur. This technological advancement has significantly reduced errors and rework, leading to faster turnaround times and improved customer satisfaction in auto body repair shops:
Computer-Aided Welding Systems for Accuracy
Computer-aided welding systems have revolutionized accuracy in modern auto body repair. These advanced tools integrate software and hardware to precisely control welding parameters, ensuring consistent quality across repairs. Auto body technicians now rely on these systems to achieve factory-level welds, particularly when working on complex vehicle structures.
The integration of computer-aided systems has significantly reduced human error in welding processes. By automating critical aspects such as heat input and wire feed speed, these systems maintain optimal welding conditions throughout the repair process. This level of control is especially crucial when working with advanced materials used in modern vehicle construction, such as high-strength steels and aluminum alloys.
Computer-aided welding systems also enhance efficiency in auto body shops. They enable technicians to quickly set up and execute welding tasks, reducing overall repair times. Additionally, these systems often include features for data logging and quality control, allowing shops to maintain detailed records of repairs and ensure compliance with industry standards and manufacturer specifications.
Developments in Protective Welding Gear
Modern auto body repair shops have embraced advanced protective welding gear to ensure technician safety and enhance work quality. High-tech welding helmets with auto-darkening features now protect welders' eyes from harmful radiation while providing clear visibility. These helmets adjust automatically to varying light conditions, allowing for seamless transitions between welding and inspection tasks.
Respiratory protection has significantly improved with the introduction of powered air-purifying respirators (PAPRs) in welding environments. These systems provide a continuous flow of filtered air, protecting technicians from harmful fumes and particulates generated during the welding process. The integration of lightweight, breathable materials in welding jackets and gloves has enhanced comfort without compromising protection.
Technological advancements have led to the development of smart personal protective equipment (PPE) for welders. These innovative solutions incorporate sensors that monitor environmental conditions, alerting technicians to potential hazards such as excessive heat or dangerous gas levels. Some systems even track welding parameters and work durations, helping to prevent fatigue and maintain optimal working conditions in auto body repair facilities.
Welders adapted to the new machines, their hands learning fresh rhythms. Now they faced a different challenge: mastering skills for a changing trade.
Training and Skill Development for Modern Welders

Training and skill development are crucial for modern welders in auto body repair. Specialized welding education equips technicians with advanced techniques essential for today's vehicles. Certifications validate expertise in cutting-edge welding methods, while ongoing adaptation to emerging technologies ensures welders stay current with industry advancements. These elements combine to maintain high standards in auto body repair.
The Importance of Specialized Welding Education
Specialized welding education is crucial for modern auto body repair technicians to master the advanced techniques required for today's vehicles. As automotive materials and designs evolve, welders must stay updated on the latest methods for joining complex alloys and composites. This specialized knowledge ensures that repairs maintain the structural integrity and safety features of modern vehicles.
Training programs focusing on auto body welding teach technicians how to work with high-strength steels, aluminum, and other advanced materials used in contemporary vehicle construction. These courses cover specific techniques like resistance spot welding and MIG welding, which are essential for repairing components such as body panels and structural elements. By gaining expertise in these areas, welders can perform repairs that meet manufacturer specifications and safety standards.
Specialized education also emphasizes the importance of understanding the impact of welding on vehicle systems. Modern cars contain sensitive electronics and safety features that can be affected by improper welding techniques. Through comprehensive training, welders learn to navigate these challenges, ensuring that repairs do not compromise the functionality of critical systems like airbags or advanced driver assistance technologies.
Certifications for Advanced Welding Techniques
Certifications for advanced welding techniques play a crucial role in modern auto body repair. These certifications validate a welder's expertise in cutting-edge methods, ensuring they can handle complex repairs on today's sophisticated vehicles. Auto body shops often require technicians to obtain certifications from recognized organizations to maintain high standards of quality and safety.
Advanced welding certifications typically cover specialized techniques such as aluminum welding, high-strength steel welding, and advanced joining methods. These programs often include rigorous testing of both theoretical knowledge and practical skills, ensuring that certified welders can apply their expertise in real-world repair scenarios. Certifications may also focus on specific welding processes like MIG or TIG welding, which are essential for repairing modern vehicle components.
Continuous recertification and updating of skills are essential aspects of advanced welding certifications in the auto body repair industry. As vehicle technologies evolve, welders must stay current with new materials and techniques. This ongoing process of skill development and validation ensures that certified welders can meet the challenges of repairing increasingly complex vehicle structures:
- Specialized certifications for aluminum and high-strength steel welding
- Rigorous testing of theoretical and practical skills
- Focus on specific welding processes like MIG and TIG
- Continuous recertification to stay current with industry advancements
- Validation of expertise in cutting-edge repair methods
Adapting to Emerging Welding Technologies
Auto body repair technicians must continuously adapt to emerging welding technologies to stay competitive in the industry. As vehicle manufacturers introduce new materials and construction techniques, welders need to update their skills regularly. This adaptation often involves learning to use advanced equipment such as laser welding systems or friction stir welding machines, which require specialized training and expertise.
The integration of computer-aided welding systems in auto body shops necessitates technicians to develop digital literacy skills. Modern welders must become proficient in operating software-driven welding equipment, interpreting digital blueprints, and analyzing welding data. This technological shift requires auto body professionals to blend traditional welding knowledge with new-age digital competencies, ensuring they can effectively utilize cutting-edge repair techniques.
Emerging technologies like augmented reality (AR) are revolutionizing welding training and on-the-job guidance. AR systems can provide real-time instructions and feedback during welding processes, helping technicians perfect their techniques. Auto body repair shops investing in these technologies enable their welders to quickly adapt to new methods and maintain high-quality standards across various repair scenarios, ensuring customer satisfaction and vehicle safety.